Hi Sewing Friends,
Happy Independence Day! I just got back from a trip to Chicago where I had the pleasure of visiting one of my all-time favorite fabric stores. The silks and stretch knits that they stock are nearly impossible to find in Florida so after a 5 hour shopping spree, my yearly stock-up mission of stretch bamboo knits and luxurious silks was accomplished! Visiting fabric stores while traveling is often the highlight of my trip punctuated by pleasant memories when I use the material and wear the garments. Be sure to tune in to our next Today’s Special on August 11th when I’ll be wearing some of my “Fall Fashions–2010” made with fabrics from my mini vacation!
RE-NEW Here’s a fast and easy way to add a spark of personality to a tired old Tee-Shirt. The new addition of a scarf can add a colorful trendy update to one of your gently worn tees from last season. The tie can be made from a scarf from your accessory stash or from a new piece of cut silk. Either way the surface interest and feminine flair are sure to get you noticed!
You have to start with a tee that has a wide enough neckline band to support buttonholes and a 4″ x 60″ strip of lightweight silk. (I used a new cut piece from a 45″ wide bolt but would choose a wider silk when repeating this project for a longer tie)
Serge or roll hem the edges of the silk strip. I had the best results using the rolled hem foot on my Quantum L-500 with the integrated dual feed engaged. This kept the silk from dancing out of control under the presser foot while trying to stitch a straight line…The difference was night and day! Next time I’ll opt to serge. Press the finished scarf and set aside.To prevent fabric jams and warped buttonholes, cut 1″ x 6″ strips of iron-on tear away stabilizer and press with a hot iron onto the backside of the neckline band. This is necessary to support the stretchy band and keep it in place while stitching the buttonholes.
Mark buttonhole placement
Make sure that
1) upper and lower thread colors match so they will blend into the tee-shirt knit and allow the silk scarf to be the star and
2) change to a ballpoint needle.
Make a practice buttonhole on a scrap of fabric to determine the size. 1/2″ in length is plenty. Stitch buttonholes over the markings. Carefully cut open the buttonholes. Lace the finished silk strip through the openings and tie.
EMBROIDERY
Have you been hearing the buzz about appliqué embroidery? This is an interesting technique that incorporates fabric cutouts with embroidery designs. Fabric color is used as a block fill instead of stitches. Some embroidery CDs come with the appliqué fabric already laser cut with a heat activated fusible backing. You can also make your own appliqués when a design has an independent block that has an outline stitch. There are a few inherent challenges when doing applique embroidery. 1) Line up your fabric piece inside the outline stitch exactly to incorporate it into the design. 2) removing the hoop and pressing the aaplique in place, then replacing the hoop and continuing where you left off. (I skip this step and show you how below)
Following are a few of my favorite tips and tricks for successful machine embroidery appliqué when you don’t have specific laser-cut pieces for a design. These tips are your keys to success. You will NOT have to unhoop to press the appliqué in place or even remove the hoop at all! You also won’t have to struggle to press the appliqué into place with the large cumbersome tip of a conventional iron. Consider using appliqué embroidery as a topper to control fabric loops peeking through when embroidering terry cloth and other napped fabrics.
SUPPLIES:
* Small scraps for applique backed with fusible adhesive paper such as Heat N’Bond found in Sewer’s Friend Adhesive Kit item # 434-662
* Clover Mini Iron, item # 914465
* Embroidery design with an outline block
* Iron-On Tear/Away Quilters Freezer paper sheets item # 105-77551. Press iron-on tear away ( or the shiny side of freezer paper) on to the top side of your project where you want the design and hoop the area with the paper. Place the hoop on your machine.
2. While the iron is hot, Press the heat activated adhesive paper to the underside of your appliqué fabric.3. Forward the color blocks to the ‘outline’ blocks and stitch them first. Gently make an identifying mark on the
paper over the appliqué area with a pencil so you will
be able to identify the topside of the pattern and avoid cutting out an applique wrong side up.
4. Carefully remove the perforated paper and set it aside to use as a pattern.5. Place the small pattern pieces on top of the appliqué fabric’s right side.
6. Trace the pieces and cut them out around the trace markings.
7. Remove the paper backing and place the pieces inside the matching outlines in the hoop.8. Use a mini iron to press the appliqué in place.
9. Continue working your way through the remainder of the embroidery design.
If the silver lame shield background had been eliminated, you would see the cream terry cloth poking through between the gray shield markings. The use of fabric in embroidery as a fill can add more variety and surface interest to your designs
NEEDLE KNOW-HOW!
Sewing machine needles may seem overly complex or ridiculously simple, depending on how you look at them. There are more parts to them than meet the eye (no pun intended) , but once you understand how each part relates to another, the needle becomes another useful tool that you can use to create timeless heirlooms or wearable art – or a combination of the two!
The shank is the part of the needle that is usually hidden from view, as it is the part that is inserted into the machine. It usually has a rounded front and a vertical, flat back. This design is utilized to prevent inserting the needle incorrectly – it will only fit one way, and is essentially foolproof. The shaft is the part of the needle below the shank; it encompasses everything that is not hidden within the machine.
On the back of the needle (on the same side as the flat part of the shank), there is an indentation just above the eye of the needle that is known as the scarf. The scarf serves multiple purposes, depending on its length. A longer scarf helps the bobbin hook grab the sewing thread more easily, and thereby reduce the number of skipped or missing stitches. A shorter scarf is used with machines that are more precisely timed, since the bobbin won’t need as much help on those systems.The point is the part of the needle you’re likely already quite familiar with, especially if you’ve ever hand-stitched a particularly dense fabric! Like handheld needles, the point on a sewing needle is the sharp pointy section of metal that passes through the fabric and guides the thread to the bobbin. Different types of needles will have different points, but all of them serve the same primary purpose.
Just above the eye of the needle is a small slit, known as the front groove. The front groove is there to help guide the thread into the eye and therein ensure a smooth stitch. Finally, the eye of the needle is the oval-shaped hole in the point where thread passes through. As with the point, the eye will vary according to the type of needle and the purpose it’s designed for.
Now that you’re familiar with the parts of a needle, let me give you a quick overview of the different types of sewing machine needles that you’ll encounter:
- Regular Point Needle – this is the needle that you’ll use most often, as it’s made for all woven fabrics.
- Ball Point Needle – a ball point needle is used when you are sewing knit fabrics, or fabrics that curl when damaged. The ball on the point of this needle (hence the name!) separates the threads of the fabric when it stitches, which saves the machine from skipping stitches or tearing fabric fibers as you sew.
- Chromium Regular Point and Chromium Ball Point Needles – these needles serve the same purpose as their aforementioned counterparts, but the difference is that it is a slightly stronger needle and will last longer, which is ideal for embroidery machines as they tend to stitch at a higher speed than traditional machines.
- Denim or Jeans Needle – as the name suggests, this needle is designed to sew heavy fabrics such as denim, canvas and poplin.
- Twin Needle – mainly used in decorative stitching on wovens, this needle is able to stitch two rows of straight or decorative satin stitches at the same time!
- Hemstitch Needle or Wing-Needle – this needle is a favorite of naturally woven fiber fabrics because it gently creates a hole in the fabric as it sews giving the stitch a vintage look.
- Wedge-Point Needle – if you’re making a motorcycle jacket, this is the needle for you! It’s designed to punch through hard materials like leather or heavy vinyl.
If you’re unsure of exactly which needle to use, double-check your needle packaging – it’ll usually tell you what fabrics will work with your chosen needle. Knowing which needle to use for your project is a valuable skill to learn for any sewer. Many generic problems like fabric snags and holes or uneven/skipped stitches are due to using the incorrect needle for the type/weight of fabric.
COMPUTER TIP!
You may have a special feature on your sewing machine known as the infinity/continual stitch button.
It is represented on a menu button by a graphic of horizontal dots …..
Here’s how it works:
If you were to choose one of the decorative stitches, for example a satin stitch triangle, many of the computers would stitch ONE decorative triangle and then stop——-but when you choose the triangle and then push the infinity button and begin sewing, the machine will stitch consecutive triangles one after the other without stopping in between.
It’s nice to have the option of single patterns or many in a row.
What’s New???

JULY 6 1 pm, 7 pm
JULY 10 2 am, 7 am, 6 pm
JULY 11 4 am, 2 pm

- 1700 watts of power
- A Brushed stainless steel soleplate
- Advanced LCD electronic temperature with 9 settings
- Vertical and horizontal bursts of steam
- 3 way auto-shut off
- Anti-drip
- Open Soleplate tip and 360* cord rotation
Item # 960-258 $74.95 FREE S&H
WHEN TO WATCH SEWING
August 11th – A new SINGER Sewing Machine TODAY’S SPECIAL
12 Midnight, 1am, 5am, 7am, 8am, 10am, 2pm, 6pm, 7pm, 11pm
Sew Your Summer Sensations,
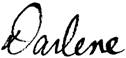